Comunicación presentada al V Congreso de Smart Grids
Autores
- José Mª Torre-Marín Martínez, Jefe Área Biofactorias, Empresa Mpal. de Abastecimiento y Saneamiento de Granada
- Juan Antonio Vico Jiménez, Jefe Biofactoría Vados, Empresa Mpal. de Abastecimiento y Saneamiento de Granada
- Marcos Antonio Martínez Martínez, Dir. Operaciones, Empresa Mpal. de Abastecimiento y Saneamiento de Granada
Resumen
Este nuevo modelo de gestión nos ha permitido transformar la EDAR Sur de Granada en la Biofactoría Sur Granada, ya que, gracias a los principios de la economía circular, podemos ser capaces de generar recursos de calidad a partir de los residuos. Es decir, pasamos de hablar de un modelo de búsqueda de la eficiencia en el tratamiento de los recursos, a buscar el concepto de biofactoría, es decir, la sostenibilidad en la recuperación de recursos (pasamos de ser consumidores de energía a productores de energía, valorizamos el 100% de los residuos y reutilizamos el 100% del agua depurada).
Palabras clave
EDAR, Biofactoría, Autosuficiencia, Energía, Biogás, Cogeneración, Economía Circular
Introducción
El entorno actual es cambiante y exige el planteamiento de nuevos retos, llevar a cabo actuaciones con impacto local para dar respuesta a retos globales. El éxito no es posible sin la creación de acuerdos, de alianzas donde cada actuante aporte conocimiento y herramientas. La vertebración y desarrollo de las ciudades evoluciona a través de las distintas actuaciones promovidas por los integrantes de la sociedad, muchas de las cuales no siempre son visibles o conocidas. La evolución experimentada por la EDAR Sur de Granada es un claro ejemplo. Un cambio de mirada ha originado la transformación de dicha estación en una Biofactoría. Ya no se trata de extraer, producir, comprar, usar y tirar. Se trata de entender el mundo como a un ser vivo, como un sistema de interrelación e interdependencia. La economía circular en vez de destruir construye capital social, natural y económico.
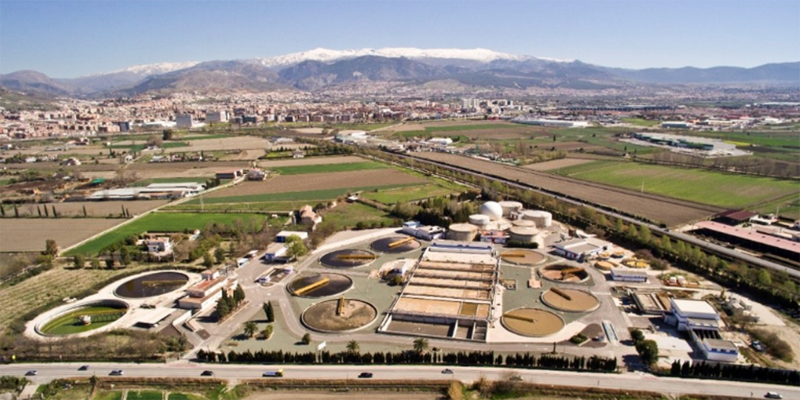
Este nuevo modelo de gestión nos ha permitido transformar la EDAR Sur de Granada en la Biofactoría Sur Granada, ya que gracias a la economía circular podemos ser capaces de generar recursos de calidad a partir de los residuos. Es decir, pasamos de hablar de un modelo de búsqueda de la eficiencia en el tratamiento de los recursos (minimización de residuos, eficiencia en el consumo, eficiencia en los costes de producción) a buscar el concepto de biofactoría, es decir, la sostenibilidad en la recuperación de recursos (pasamos de ser consumidores de energía a productores de energía, valorizamos el 100% de los residuos y reutilizamos el 100% del agua depurada). La propuesta circular de aprovechamiento de recursos en la Biofactoría Sur Granada, tiene tres objetivos fundamentales:
- Crear un beneficio para el medio ambiente mediante la autoproducción de energía y autosuficiencia y recuperación de residuos con el foco global de la neutralidad en carbono.
- Mitigar los riesgos producidos por los impactos que genera la actividad de depuración, ya sean ambientales (p.e. descarga de contaminantes al medio), sociales (p.e. generación de olores) o económicos (p.e. variabilidad en el precio de la energía).
- Ser un referente empresarial del concepto de economía circular, sin olvidar los aspectos sociales y de biodiversidad.
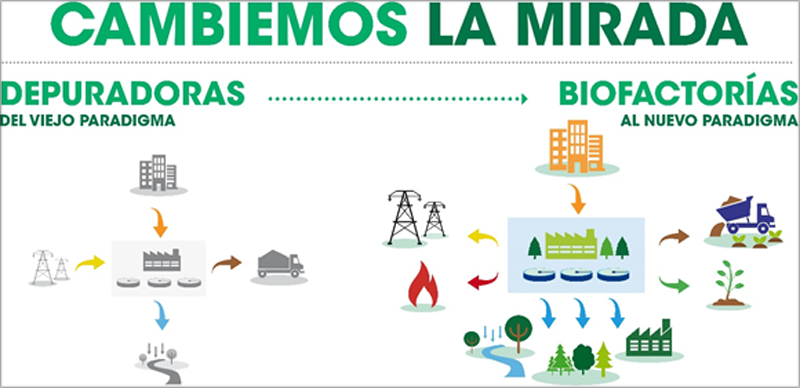
Proceso
Para minimizar el impacto energético, Emasagra ha trabajado históricamente en la eficiencia energética de equipos e instalaciones tras evaluaciones específicas de su infraestructura. Además, con ánimo de dar un paso más en este sentido, mejora sus infraestructuras generadoras de energía renovable e implementa nuevas acciones que permitan el autoconsumo, de tal modo que en conjunto se obtenga un balance energético nulo o positivo en cuanto a emisiones a la atmósfera. En lo relativo al objetivo de autoabastecimiento energético de la Biofactoría Sur Granada, para llegar a alcanzar el 100% de autoabastecimiento, e incluso superarlo, es preciso destacar las numerosas actuaciones llevadas a cabo con el fin de reducir el consumo energético y a su vez mejorar la eficiencia.
Los hitos que seguidamente se indican, han sido desarrollados en las diferentes líneas que se integran dentro del proceso de la depuración de aguas residuales.
Principales hitos línea de agua
2010 – Instalación de nuevos equipos de agua bruta
La primera etapa en la depuración de aguas residuales en la Biofactoría sur es elevar la cota del agua unos 5,79 metros para poder continuar el proceso de depuración por gravedad, evitando así continuos bombeos entre equipos. Esto se consigue mediante tornillos de Arquímedes, un sistema muy simple y duradero para elevar agua que contenga cualquier tipo de sólido. Inicialmente se encotraban instalados: 2 tornillos de 950 m3/h, 2 tornillos de 1044 m3/h y un tornillo de 1800 m3/h, se decidió instalar sustituir un tornillo de 950 m3/h por uno de 1800 m3/h, respecto a la potencia instalada, los cuatro tornillos de mayor antigüedad tienen motores de 37kW y el nuevo tornillo se instaló con un motor de 45kW. Siendo por lo tanto más eficiente priorizar el funcionamiento de los tornillos de mayor capacidad de elevación en caudales punta, optimizando de esta manera el consumo energético.
2011 – Instalación de nuevo decantador primario
En la decantación primaria se reduce al menos un 20% de DBO y un 50% de sólidos en suspensión del agua residual. El aumento del rendimiento de esta etapa conlleva tres ventajas desde el punto de vista de balance energético (Brandt et al., 2010):
- Reduce la carga orgánica del tratamiento secundario, ahorrando por tanto energía en la aireación.
- Reduce la cantidad de fango activo secundario, el cual puede requerir más energía para su tratamiento.
- Aumenta la producción de fango primario, el cual tiene una concentración superior en materia orgánica biodegradable y fácilmente produce el doble de biogás que el fango secundario activado en un digestor anaerobio (Hellstedt et al., 2010).
Se construyó un nuevo decantador circular de geometría similar a los tres existentes (28m de diámetro). Estos decantadores circulares tienen instalados un motor de 1,1kW para mover el puente decantado. Por lo tanto, en consumo energético en esta etapa es muy bajo comparado con la mejora de eficiencia en esta etapa del proceso, consiguiendo significativos ahorros en el consumo energético en aireación y mejora en la producción de biogás, que se utiliza en el proceso de cogeneración.
2012 – Instalación de soplantes de levitación magnética
Para mantener el reactor biológico en óptimas condiciones se necesita un aporte constante de materia orgánica (agua residual) y oxígeno (mediante aireación). La aireación en esta etapa se producía por turbosoplantes de émbolos rotativos, cuyo funcionamiento no permitía adaptarse a las necesidades de aire cambiantes que necesitaban los reactores biológicos. Mediante su sustitución por soplantes de levitación magnética, se consiguió mejorar la ratio Nm3aire/kWh, por lo que se necesita un menor consumo energético para impulsar la misma cantidad de aire.
2013 – Automatización de la aireación
Para que el reactor biológico esté funcionado en óptimas condiciones, de acuerdo con la experiencia que tiene Emasagra, es recomendable mantener el nivel de oxígeno en 1 mgO2/L. Existían oxímetros midiendo en continuo la cantidad de oxígeno disuelto y era el operador de proceso el encargado de actuar sobre la válvula que permitía regular el flujo de aire hacia los distintos reactores. Esto era muy ineficiente, ya que le suponía un gran volumen de trabajo y casi una dedicación exclusiva a esta tarea. Mediante la automatización mediante válvulas motorizadas, a raíz de la consigna anteriormente indicada, mediante un PLC se actuaba de forma autónoma sobre las válvulas de aire, evitando las sobrealimentaciones de aire y manteniendo unas condiciones constantes de proceso, redundando en un ahorro energético.
2015 – Renovación de las parrillas de difusores
El aporte de aire a los reactores biológicos se consigue a través de los soplantes de levitación magnética, pero la transmisión de oxígeno al agua se consigue por medio a los difusores de burbuja fina. Es importante generar uan burbuja fina, ya que la superficie de contacto para maximizar la transferencia de oxígeno a los microorganismos es mayor que en la de burbuja gruesa. Es habitual que con el tiempo las membranas de los difusores se desgasten y pierdan eficiencia, generando cada vez una burbuja de mayor tamaño. Sustituyéndo las membranas se consiguió disminuir la necesidad de aire para mantener el nivel objetivo de oxígeno disuelto, lo que se traduce en menor cantidad de Kw consumidos en la aireación.
2015 – Análisis de rendimientos de tornillos agua bruta y uso predeterminado de los más eficientes
El caudal de agua residual que recibe la Biofactoría no es constante a lo largo del día, hay momentos que el caudal es mínimo y periodos de caudal máximo horas punta de recepción de agua. por lo que una vez analizados los m3bombeados/kW en los tornillos, se ha priorizado el funcionamiento de unos sobre otros dependiendo de la cantidad de agua residual que llega a la instalación, optimizando de esta manera el consumo energético en el proceso de elevación.
2016 – Limitación del número de soplantes en servicio, dependiendo del periodo horario
El funcionamiento de los soplantes, al igual que otros equipos como bombas, compresores, etc. tiene un punto óptimo de operación, fuera de ese punto el ratio de aire producido frente al consumo energético pierde eficiencia, por lo tanto, se programa el funcionamiento de las soplantes para que siempre funcionen en el punto óptimo de producción de aire.
2016 – Parada de Trafos para evitar consumos innecesarios
Es habitual tener equipos de respaldo en las instalaciones, y en nuestro caso se dispone de trafos en reserva, pero su conexión de manera permanente, aunque no estén suministrando energía, suponía un consumo energético fácilmente evitable. Simplemente se desconectaron, pero guardando la precaución de volver a reconectarlo de forma sencilla y rápida si las condiciones así lo requerían.
Principales hitos línea de fangos
2014 – Modificación del régimen de agitación de digestores
Es muy habitual encontrarse con condiciones de funcionamiento que se han mantenido a lo largo del tiempo, pero sin cuestionarse si era eficiente para instalación. En el caso de la agitación de los digestores anaerobios, esta se realiza inyectando gas a presión mediante lanzas en el interior del digestor, y el aumento de presión se produce en los compresores de biogás.
En nuestro caso se estudiaron distintas condiciones de agitación, reduciendo las horas de agitación y analizando la cantidad de biogás producido, concluyendo que no era óptimo agitar las 24 horas del día, sino que con una hora de agitación y 4 de reposo, se producía la misma cantidad de biogás, el cual posteriormente será utilizado en el proceso de cogeneración para el autoabastecimiento energético de la instalación.
Principales hitos línea de gas
2015 – Aumento de secciones en red de biogás aumentando la capacidad de transporte
El biogás producido en los digestores anaerobios es almacenado en los gasómetros previo a su valorización en los motores de cogeneración. Por seguridad, en la línea de biogás hay instaladas válvulas de sobrepresión. Se identificó que en ocasiones entraban en funcionamiento. Se analizó el problema y se determinó que la sección de la tubería de biogás era insuficiente, lo que suponía un cuello de botella que producía sobrepresiones. Duplicando la sección de las conducciones se eliminaron las sobrepresiones y se aprovecha el 100% del biogás generado.
2015 – Aprovechamiento energético para instalación de electrolinera
Se trata de la instalación de una electrolinera en la Biofactoría, que consta de dos plazas dotadas con sus respectivos cargadores eléctricos de 22 Kw/ud, donde se realizan las recargas de las baterías de los vehículos eléctricos adquiridos recientemente por Emasagra, y de esta manera impulsar el uso de vehículos eléctricos, con el beneficio medioambiental que implica el uso de energía limpia generada en la Biofactoría.
2018 – Adquisición de nuevo motor de cogeneración de 600 kWe
En el año 2001 se pusieron en funcionamiento dos motores Guascor de 250 kWe con un rendimiento eléctrico del 28%. Durante este tiempo, todo el biogás generado se ha valorizado en estos motores produciendo energía eléctrica para el autoabastecimiento, y la energía térmica se recuperaba de los gases de escape y de la refrigeración de las camisas del motor, todo ello con el objetivo de compensar las pérdidas térmicas de los digestores anaeróbicos. Este año se ha instalado un motor MWM de 600kWE con un rendimiento eléctrico del 41,6%, de manera que con el mismo biogás, se consigue producir más energía eléctrica llegando a valores del 100% de autoconsumo.
Resultados
De acuerdo con los datos registrados, se puede observar una reducción importante del consumo energético de la instalación, todo ello de conforme a la ejecución de las mejoras realizadas en todas las líneas de proceso. Así mismo, se puede observar una mayor producción de energía cogenerada, gracias a un incremento de la cantidad de biogás generado, de acuerdo a las mejoras realizadas tanto en la línea de fango como en la línea de gas.
El valor promedio de autoabastecimiento de energía real desde enero-18 a agosto-18 ha sido de un 92,5%. Igualmente es destacable que durante los meses de marzo-18, abril-18 y julio-18, se ha superado el 100% de autoabastecimiento de energía, llegando a ser en abril-18 de un 122%.
En la siguiente gráfica se puede observar que la concentración de materia orgánica de entrada en la instalación, se mantiene constante, asi como la concentración de salida se mantiene en niveles muy por debajo de los valores máximos admisibles indicados en la autorización de vertido. Igualmente, el caudal de agua bruta de entrada, también se mantiene constante, siendo las leves variaciones en este parámetro, las debidas a las mayores o menores precipitaciones.
Conclusiones
Durante los meses de marzo, abril y julio de 2018, se ha superado el 100% de autoabastecimiento energético, alcanzándose el gran reto de llegar a ser una biofactoría autosuficiente energéticamente, teniendo en cuenta que se han mantenido estables, e incluso se han mejorado los rendimientos en la eliminación de contaminantes, así como se han mantenido los caudales tratados.
La consecución de este logro, es debida al respaldo de la dirección de la empresa, comprometida con el desarrollo sostenible, dando la posibilidad de implementar todas aquellas mejoras anteriormente citadas en los equipos e instalaciones que han permitido reducir sistemáticamente el consumo de energía e incrementar la producción de energía cogenerada.
Referencias
- Brandt, M., Middleton, R., Wang, S. 2010. Energy Efficiency in the water industry. A compendium of best practices and casestudies. Global Report. UKWIR Report Ref. No 10/CL/11/3. London.
- Hellstedt, C. et al. 2010. Increased biogas production at the Henriksdal Wastewater Treatment Plant (WWTP). BIOGASMAX – Integrated Project No 019795.